【メッキ技能士直伝】摺動性とはどんな性質。摺動性を高める表面処理の選択
- コネクション
- 2024年9月14日
- 読了時間: 11分
更新日:3月25日
機械部品などに要求される性質の一つとして、摺動性があります。
摺動性とは、物体同士が接しているときの滑りやすさのことです。
摺動性は摩擦が小さいほど良く、機械などで部品同士が接しているときには必要な性質です。
摺動性を高くするためにはさまざまな方法があり、活用されています。
本記事では、その中でもメッキなどの表面処理による方法に着目し、解説していきます。
なお、メッキは専門的な技術ですので、弊社のような専門業者にご相談の上、活用してください。
■INDEX■
1.1.摺動性とはどんな性質?
1.2.摺動性が求められる場面
1.3.摺動性が高いことによるメリット
2.1.材料の選択
2.2.表面処理
2.3.潤滑剤の使用
2.4.形状の工夫
3.1.硬質クロムメッキ
3.2.無電解ニッケルメッキ
3.3. フッ素樹脂コーティング
3.4. 複合メッキ
4.1.使用環境や素材
4.2.要求特性
4.3.コスト
1.摺動性とは
1.1.摺動性とはどんな性質?

摺動性という性質は、2つの物体が接しているときに求められる性質で、接した2つの物体が相対的に動くときの滑らかさを指します。
摺動性が大きいと摩擦や摩耗が少なく、その機械の効率や機械寿命に影響してしまいます。
物体同士が動くときの滑らかさはその物体同士の摩擦係数や物体表面の硬度に関連し、機械などで摺動性が求められる摺動部には、特にこれらの性質が重要となります。
1.2.摺動性が求められる場面
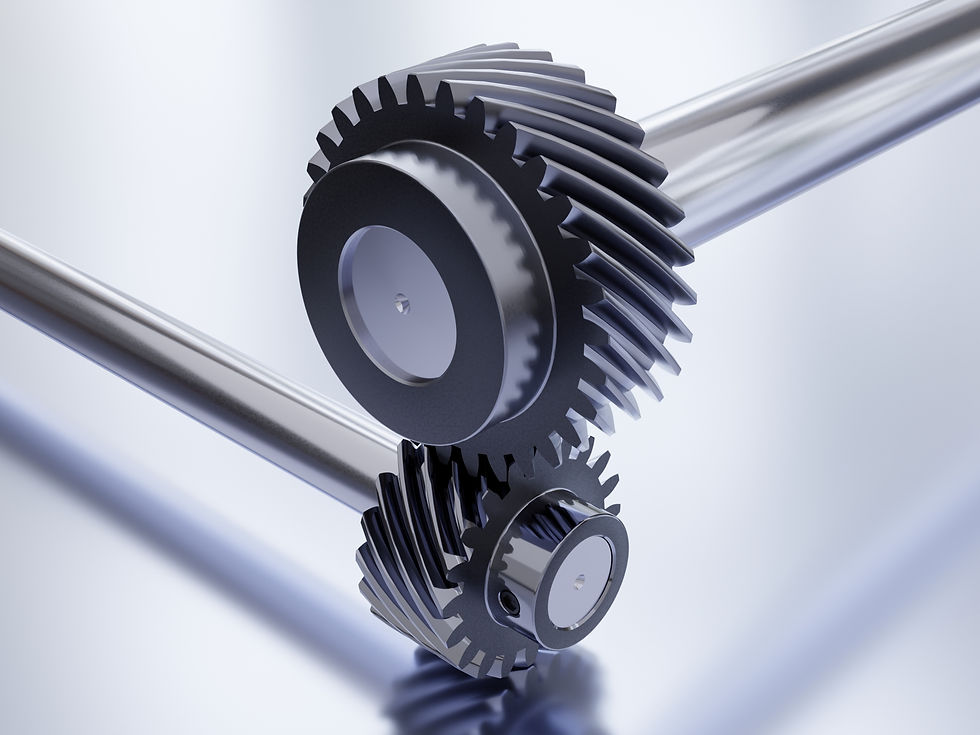
摺動性が求められる場面として、いくつかの事例をご紹介します。
・軸受(ベアリング):軸と軸受の間を滑らかに動くようにし、回転をスムーズにする必要がある。
・歯車(ギア):歯車同士は滑り接触なので、それぞれの滑りを良くして動力を伝えやすくする必要がある。
・スライド機構:部品の直線運動を摩擦損失を少なく伝える必要がある。
・自動車部品:エンジン内部、ブレーキシステムなど、摩擦によるエネルギー損失を抑える必要がある。
他にもさまざまな場面で摺動性は必要になることがあり、部品に摺動性を高めるためにさまざまな方法が適用されます。
1.3.摺動性が高いことによるメリット
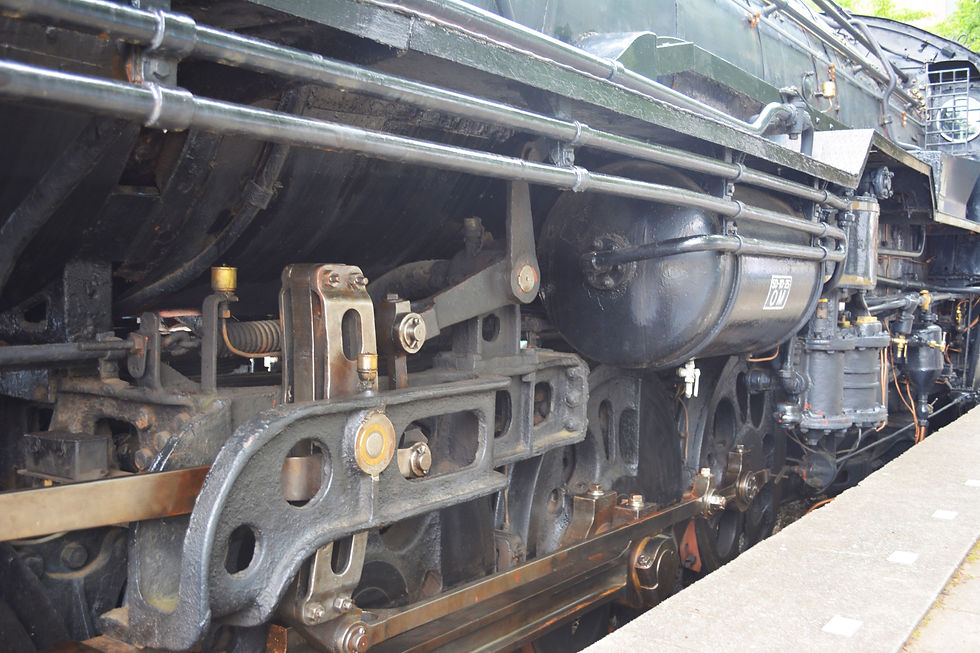
摺動性が高いことにより、まず第一に摩擦によるエネルギー損失を減少させることができます。
このことにより、省エネルギーや自動車部品などでは燃費向上などにも繋がります。
また、部品の消耗が少なくなることから、部品寿命が長くなり、メンテナンス性も向上します。
動作するときに静音となり、さらに機械操作性を向上させることにも繋がります。
摺動性は、機械効率、寿命、操作性など広い範囲でとても重要な役割を果たす性質なのです。
2.摺動性を高くする方法
2.1.材料の選択

摺動性を高くするにはいくつかの方法が考えられます。
まず一つは、そもそも摺動性の高い材料を選択することです。
例えば、テフロンやナイロンなどです。
これらの物質を材料に選んでおけば、材料同士が接触する部分も当然摺動性の良い性質を持つことができます。
ただし、物体の材料というのは摺動性のみを根拠に選ぶものではないことがほとんどです。
材料の強度をはじめとして、さまざまな性質を鑑みたとき、必ずしもテフロンやナイロンをどこにでも使えるわけではありません。
2.2.表面処理
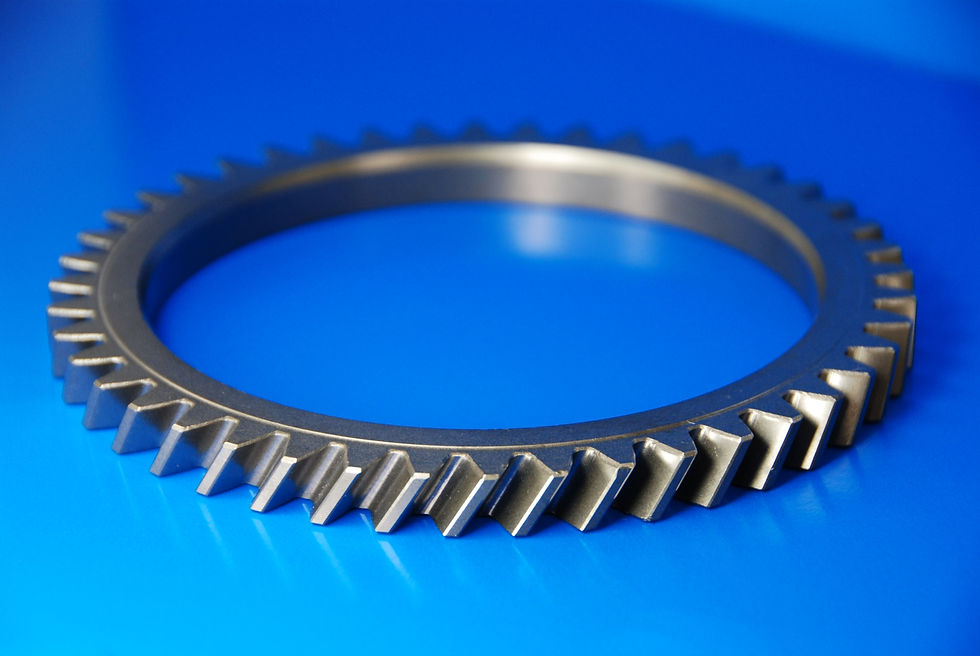
強度など摺動性以外の理由で材料に金属材などを採用した場合、そのまま使用したのでは求められる摺動性が得られない場合があります。
そのような場合でも、接触し合う材料同士の表面が摺動性を持っていれば、機械そのものの摺動性を保つことができます。
そこで、そのような金属材料に表面処理を行う方法もあります。
表面処理とは、素材表面にのみ処理を施して、素材の表面のみに素材の性質以外の性質を付与する技術です。
摩擦が大きな金属材料などにおいても、表面だけを潤滑性を上げたり、硬度を高くすることによって、摺動性を付与することができます。
摺動性の問題を解決したい場合、なにも素材全体にこだわらなくとも、この表面処理で解決するケースがほとんどです。
2.3.潤滑剤の使用

潤滑剤を使用することも有効です。
よく用いられるのは潤滑油です。
摺動部の表面に油を差すことによって、その間の摩擦係数が減り、摺動性が向上します。
自動車のエンジンオイルなどもこの効果を期待しています。
ただし、油は定期的に差したり循環させる必要があるため、この方法を取る場合はしっかりしたメンテナンス体制も必要となります。
2.4.形状の工夫

また、同じ材料でも、形状を工夫することによって摺動性を向上させることも可能です。
例えば、材料の表面に凹凸が多いと、それを横にすべらせようとしてもなかなか抵抗が大きくなることが想像されます。
また、材料同士の接触面積が大きいと、やはり滑りが悪くなってしまいます。
したがって、材料をできるだけ凹凸の無いように研磨することや、接触面の面積を小さく工夫することも有効です。
エッジ部分がある場合はエッジにアールを付けて丸めることも有効な方法です。
歯車の形状などは、これらの形状的性質を上手く組み合わせて設計されたものが多いです。
3.摺動性を高めることができる表面処理
3.1.硬質クロムメッキ
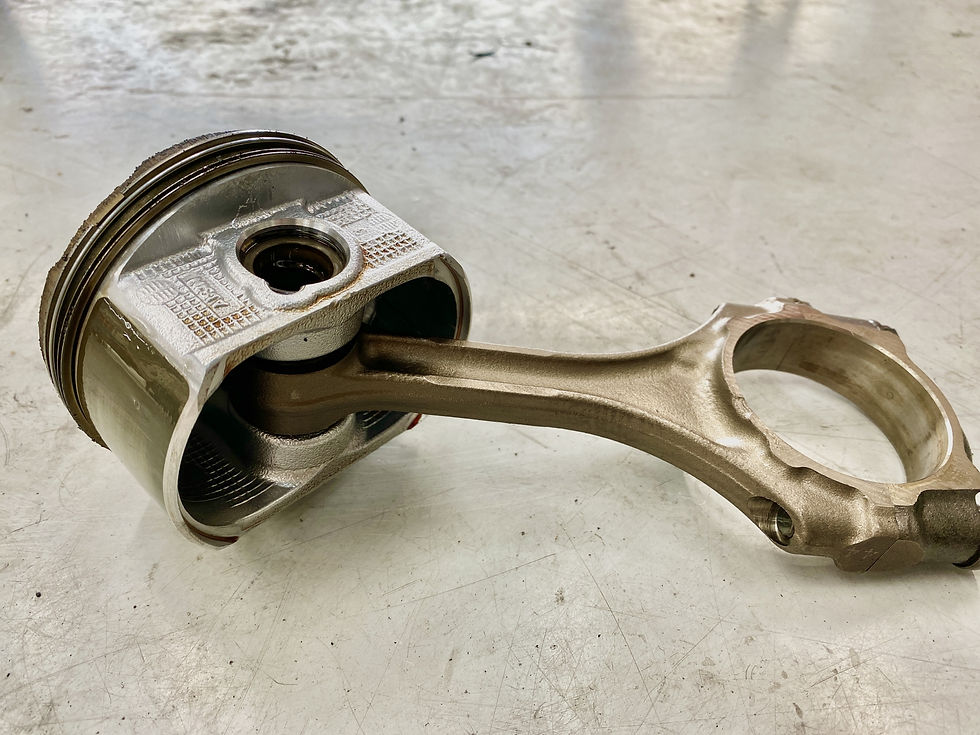
先で述べたように、摺動性を高くするには表面処理がとても有効です。
中でも摺動性を高くできる表面処理方法をいくつかご紹介します。
まず最初は硬質クロムメッキです。
メッキとは、素材に金属皮膜を生成させる表面処理のことです。
硬質クロムメッキは、メッキ皮膜が非常に硬く、そのことにより耐摩耗性も高くなります。
摺動性も高く、ピストンリング、シリンダーライナー、油圧機器部品など、高温・高圧下で摺動する部品に広く使われています。
ただし、硬質クロムメッキ同士を摺動させてしまうと、双方の部品同士でかじり現象を起こしてしまい、かえって摩耗が早くなってしまうので、注意が必要です。
そのため、摺動部の2つの部品の片方を硬質クロムメッキに、片方を交換部品に設定することがベターな方法です。
また、硬質クロムメッキはいわゆる電解メッキという方法で、この方法ではすべての表面に均一なメッキを行うことができません。
穴部やポケット部などへの均一なメッキが難しくなることも硬質クロムメッキのデメリットです。
3.2.無電解ニッケルメッキ

次に無電解ニッケルメッキです。
無電解ニッケルメッキもメッキ皮膜の硬度が高く、耐摩耗性も高く、また耐食性にも優れる他に、導電性なども付与できる表面処理です。
また、この方法は通電せずに化学的な方法でメッキを行う無電解メッキであり、無電解メッキは複雑な形状の材料にも均一にメッキができることが特徴です。
したがって、硬質クロムメッキでは困難だった穴部やポケット部などにも摺動性を付与することが可能です。
そのため、ベアリング、ギア、金型など、精密な形状が求められる摺動部品にも活用されています。
ただし、無電解メッキは電解メッキに比べて、処理時間を要し、コストも上がってしまうことがデメリットです。
3.3. フッ素樹脂コーティング

フッ素樹脂コーティングも摺動性を高くする表面処理の一つです。
母材にフッ素樹脂を粉体塗布し、加熱によって溶融させることで皮膜を生成する方法で、前述2つのメッキとは工程が違います。
皮膜そのものが非常に低い摩擦係数を持ち滑りやすく、摺動性に優れています。
また、耐薬品性や耐熱性にも優れています。
一方で、金属皮膜ほどの硬度は期待できません。
3.4. 複合メッキ

複数の表面処理を組み合わせた方法を複合メッキといいます。
この方法により、いわばそれぞれの表面処理の「いいとこ取り」をすることができます。
例えば、テフロン複合無電解メッキは、無電解ニッケルメッキにPTFE(通称テフロン)の粒子をメッキ皮膜中に分散し複合共析させた方法です。
無電解ニッケルメッキの特徴である高い硬度や耐摩耗性、耐食性などを持つ上に、低い摩擦係数での摺動性も高いものとなります。
また、無電解メッキの一つであることから、皮膜の均一性も維持することができ、穴部やポケット部へのメッキも可能です。
4.摺動性を高めるメッキの選び方
4.1.使用環境や素材

メッキなどの表面処理を行うとき、摺動性を含めたさまざまなことを考慮する必要があります。
その部材の使用環境は重要な要素の一つです。
例えば、使用環境がとても腐食しやすい環境である場合、どんなに摺動性が優れていても、表面処理としての効果をあまり発揮してくれないということになります。
また、摺動部で用いる場合でも、摺動相手材との相性なども考慮しておく必要があります。
異種金属同士が表面で接触する場合、異種金属間の電位差によるガルバニック腐食という現象も起こりうるため、そのような観点からも検討する必要があります。
4.2.要求特性

メッキの特徴は表面の金属皮膜によってさまざまです。
メッキをすれば必ず素材に比べて耐食性や耐摩耗性が得られるわけでもありませんし、摺動性についても同じです。
その物体に必要な表面の性質を全て洗い出し、結果として必要なメッキ方法を選択することが必要です。
また、ポケット部や穴部がある素材の場合、無電解メッキを利用することがお勧めです。
メッキの性質については、専門の業者に相談して検討するようにしましょう。
4.3.コスト
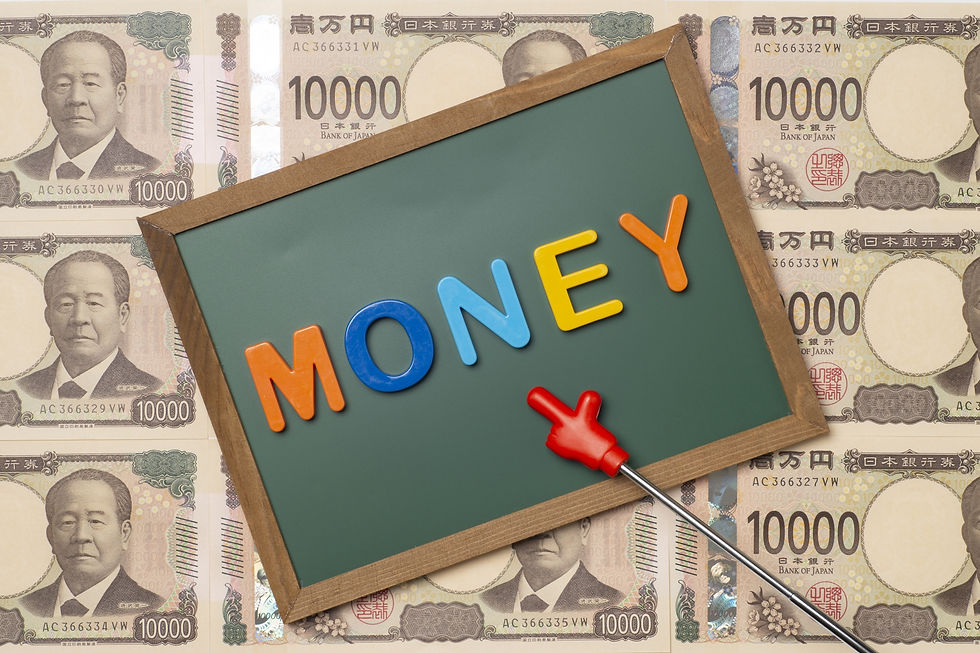
当然、コストも重要な話になります。
コストを掛けすぎて本来必要としない性質まで付与する必要はありませんが、メッキはメンテナンスの手間を省ける特徴を持つものも少なくありません。
初期費用だけでなく、メンテナンス費用までトータルで考慮したうえでベストなものを選ぶことが大切です。
こういった面も、専門の業者に相談してみましょう。
5.まとめ

機械部品などの摺動性とそれを高める方法について解説してきました。
また、中でも表面処理による方法については特に詳しく解説しました。
以下はそのまとめです。
・部品同士が接触するとき、その滑りやすさを示す性質を摺動性という。
・摺動性は、機械効率、寿命、操作性など広い範囲でとても重要な役割を果たす性質である。
・摺動性を高くするにはさまざまな方法があるが、摺動部表面の摺動性を高くする表面処理により方法は有効な方法である。
・摺動性を高くする表面処理方法には、硬質クロムメッキ、無電解ニッケルメッキ、フッ素コーティング、複合メッキなどがある。
・無電解メッキは皮膜が均一であり、ポケット部や穴部がある場合の摺動部でも高い効果を発揮することができる。
・メッキを選ぶときは、使用環境や素材、要求特性、コストなど多角的な面から専門家に相談しながら検討する方が良い。
メッキ加工のプロフェッショナルに、まずはご相談を!
「この加工、どうしても上手くいかない…」「他社で断られてしまった…」「納期が迫っているけど間に合うか不安…」そんなお悩み、ぜひ株式会社コネクションにご相談ください!
私たちコネクションは、メッキ加工や表面処理加工のスペシャリスト集団です。他社では対応が難しいとされる案件も、多くの実績と専門知識を活かして対応してきました。
他社で断られた案件こそ、私たちにお任せください!
高度な技術力: 無電解ニッケルメッキをはじめ、アルマイト処理、特注ジグを使用した加工など、様々な技術で対応します。
迅速な対応: ご依頼いただいた内容について、1営業日以内に回答いたします。急ぎの案件も、最適な解決策をご提案します。
広範なネットワーク: 100社以上の協力メーカーとの連携により、自社で難しい場合も最適な方法を見つけます。
安心のサポート体制: 実績25年以上の電気メッキ技能士が直接対応。
「自分たちの案件は無理かも」と諦める前に、ぜひ一度お問い合わせください。コネクションのスタッフが、あなたの課題に真剣に向き合い、解決に向けた最善の方法をお届けします。
お問い合わせは簡単・スピーディー!
お電話やメールフォームから、どなたでも簡単にお問い合わせいただけます。案件の概要やお悩みをお伝えいただくだけで、当社の専門スタッフが迅速に対応します。
株式会社コネクションは、「どんなメッキの悩みもまず相談してみたい!」と思われる信頼のパートナーを目指しています。ぜひお気軽にご連絡ください!
めっきに関するお問合せやご質問はメールもしくはお電話にてお気軽にご連絡下さい。
お急ぎの方はこちら 直通電話 090−6819−5609
【著者のプロフィール】
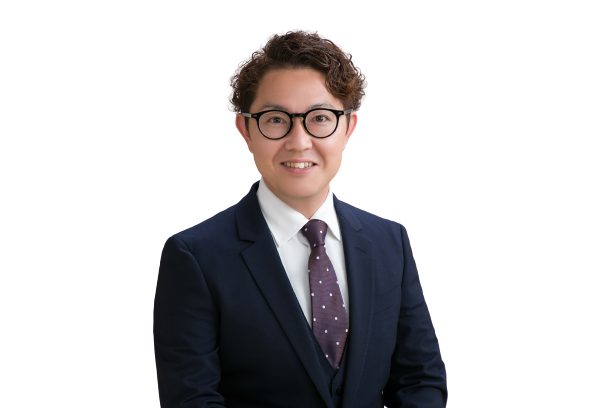
1996年、福井工業大学附属福井高等学校を卒業後、地元のメッキ専門業者に入社、製造部門を4年経験後に技術部門へ異動になり、携帯電話の部品へのメッキ処理の試作から量産立ち上げに携わる。
30歳を目前に転職し別のメッキ専門業者に首席研究員して入社。メッキ処理の新規開発や量産化、生産ラインの管理、ISO9001管理責任者などを担当。
コメント