【メッキ技能士直伝】電気亜鉛メッキと溶融亜鉛メッキの違いとは?耐用年数に違いはある?
- コネクション
- 2024年11月18日
- 読了時間: 11分
更新日:8月20日
弊社では亜鉛めっき、溶融亜鉛メッキ処理を行っています。
お気軽にお問い合わせください。
さまざまな構造や部品の防食の方法に亜鉛メッキがあります。
亜鉛メッキは、犠牲防食という特殊な方法で素材を守る防食方法で、広く一般的に用いられています。
実は亜鉛メッキには、電気亜鉛メッキと溶融亜鉛メッキの2種類の方法があります。
同じ亜鉛メッキですが、それぞれどのように使い分けたら良いのでしょうか?
また、どちらも防食用途で用いた場合、それぞれに耐用年数の違いなどはできるのでしょうか?
本記事では、いまいち混同しがちな電気亜鉛メッキと溶融亜鉛メッキのそれぞれの特徴を洗い出し、おすすめの用途をご紹介します。
亜鉛メッキの耐用年数などが気になる方も、最後まで読んでみてください。
■INDEX■
1.1.亜鉛メッキの基本的な性質
1.2.犠牲防食とは
2.1.電気亜鉛メッキの処理法
2.2.電気亜鉛メッキのメリットとデメリット
2.3. 効果的な後処理
3.1.溶融亜鉛メッキの処理法
3.2.溶融亜鉛メッキのメリットとデメリット
4.1.耐用年数
4.2.その他の性質の違い
5.1. 電気亜鉛メッキで効果が高い用途
5.2. 溶融亜鉛メッキで効果が高い用途
1.亜鉛メッキとは
1.1.亜鉛メッキの基本的な性質

亜鉛メッキは数多くあるメッキ工法の種類の中でも、多く活用されているメッキ処理です。
メッキとは、素材表面に金属の皮膜を付着させて素材を守ったり性質を付与する技術です。
中でも、鉄などの素材はそのままでは腐食しやすいため、メッキを行って腐食しにくいものにすることが多いです。
亜鉛メッキはまさに、このような防食に用いることが多いです。
また、その防食の方法には、犠牲防食という方法を取っています。
1.2.犠牲防食とは

亜鉛という金属は、鉄などに比べてイオン化傾向が大きいです。
イオン化傾向とは、酸化や還元などの反応のしやすさと密接に関わっています。
亜鉛メッキは、あえて反応しやすく酸化しやすい物質を表面に配置することで、素材を腐食から守る方法を取ります。
物質が空気などに触れ、反応して錆びてしまったりするのが腐食です。
亜鉛メッキした鉄材の場合、外側の亜鉛の皮膜が鉄よりも先に反応してゆきます。
鉄の反応、つまり素材の腐食が始まるのは、亜鉛の反応が終了してからというわけです。
防食メッキというと、表面に耐食性の高い物質の皮膜を隙間なく張り、素材を守るようなイメージもありますが、亜鉛メッキはあえて反応しやすい物質を用いることで素材を守ってくれます。
メッキ自体は犠牲になって反応するわけですから、このような防食法を犠牲防食と呼びます。
犠牲防食の場合、少々メッキに穴が開くなどの状況があったとしても、亜鉛部分さえ先に反応できるならば、役割を果たしてくれます。
広く用いられている亜鉛メッキはほとんどがこのような用途で用いられ、鉄素材の構造物の耐用年数を格段に増加させています。
2.電気亜鉛メッキ
2.1.電気亜鉛メッキの処理法

亜鉛メッキには2つの処理法があります。
電気亜鉛メッキと溶融亜鉛メッキです。
プロセスの違いにより、これら2つの方法には性質にも僅かに違いがあります。
まずは電気亜鉛メッキの処理法についてご説明します。
電気亜鉛メッキとは、メッキ液に素材を浸し、電気を流してメッキする方法です。
メッキ液内で溶けている亜鉛が電気の力で素材表面に付着し、皮膜化してゆきます。
一般に電気メッキは電気を通す素材にのみ適用でき、電気を通す鉄素材であれば電気亜鉛メッキは可能です。
皮膜の厚みは流す電気の条件や通電時間で調整することができます。
2.2.電気亜鉛メッキのメリットとデメリット

電気亜鉛メッキのメリットは、まず膜厚のコントロールをしやすい点です。
通電条件や時間から生成される膜厚も割り出すことができるため、それを調整することで膜厚も調整できます。皮膜は緻密で密着性も高いです。
光沢もあるため、見た目にも美しいメッキをすることができます。
自動車部品やネジなどの小型部品へもしっかりと皮膜が付いてくれます。
ただし、大型構造物に求められるような厚い膜厚を作ることはできません。
2.3. 効果的な後処理

電気亜鉛メッキは、後処理をすることで亜鉛自体も錆から守り、耐食性を上げることができます。クロメート処理や三価クロム化成処理です。
クロメート処理は、電気亜鉛メッキを行った製品を六価クロム酸の液に浸けることで行います。クロメート処理をすると表面の色調が変わり、白、虹色、黒など色を持たせることも可能です。
時折見かける、色が輝いて見える亜鉛メッキのネジや建材などはこの処理を行ったものです。また、環境負荷のかかる六価クロムの代わりに三価クロムを用いる三価クロム化成処理を行うことも可能です。

3.溶融亜鉛メッキ
3.1.溶融亜鉛メッキの処理法

もう一つの処理法は溶融亜鉛メッキです。
溶融亜鉛メッキは、高温で溶かした亜鉛が入った槽に素材を漬け込み、その後冷やして素材表面に亜鉛の皮膜を残す方法です。電気ではなく熱を用いたメッキ法で、ドブ漬けメッキという呼び名もあります。
皮膜にさほど緻密さはなく、見た目もザラザラしたものになります。
電気亜鉛メッキより厚く皮膜を生成させることが可能な処理法になります。
3.2.溶融亜鉛メッキのメリットとデメリット

溶融亜鉛メッキ最大のメリットは、皮膜を厚くできることです。
犠牲になる亜鉛の量が増えるということになるので、電気亜鉛メッキより耐食性が向上します。電気亜鉛メッキで適用外だった大型の構造物へのメッキも可能です。
クロメート処理などの耐食性を向上させる処理は特に必要としません。
また、筒状の製品のように、電気亜鉛メッキでは電気が流れにくいような複雑な形状にもメッキが可能です。一方で、見た目は少しザラザラしていて光沢もなく、電気亜鉛メッキと比べると劣ってしまいます。
電気亜鉛メッキのように緻密に膜厚をコントロールすることもできません。
ネジのような小型の精密部品については、形状を変えて機能性を損ねてしまう恐れもあります。メッキの際に熱を使うことから、例えば薄板の板金のようなものにメッキをすると熱変形してしまう可能性もあります。
4.電気亜鉛メッキと溶融亜鉛メッキの違い
4.1.耐用年数

ここまでご紹介してきた電気亜鉛メッキと溶融亜鉛メッキですが、プロセスの違いによってそれぞれに性質的な違いも生じます。
メッキがどの程度の年数素材を守り続けられるかを表す年数を耐用年数といいます。
亜鉛メッキの耐用年数はメッキの膜厚(付着した亜鉛量)で決定します。
耐用年数の面では、厚膜が可能な溶融亜鉛メッキに分があります。
大気中の溶融亜鉛メッキの付着量と耐用年数については、一般社団法人 日本亜鉛鍍金協会が、パターンを腐食速度の違う都市・工業地帯、田園地帯、海岸地帯で分けた形で公表しています。
膜厚の厚い溶融亜鉛メッキは550g/m2程度の亜鉛付着量が期待でき、都市・工業地帯で62年、田園地帯で113年、海岸地帯で25年程度の耐用年数を見込むことができます。
一方、それぞれの処理方法による膜厚は、電気亜鉛メッキで多くとも20μm以下、溶融亜鉛メッキは50μm以上はあるため、電気亜鉛メッキは溶融亜鉛メッキの耐用年数の40%以下しか見積もることができません。
したがって、都市・工業地帯なら電気亜鉛メッキの場合は25年程度の耐用年数ということになります。このように溶融亜鉛メッキのほうが大気中の耐用年数が高く、半永久的に使用されるような屋外の建物や構造物には適しています。
4.2.その他の性質の違い

耐用年数は溶融亜鉛メッキが優れていますが、その他の性質にも少し着目します。
例えば見た目ですが、前述の通り電気亜鉛メッキはスベスベとした光沢のある見た目なのに対し、溶融亜鉛メッキはザラザラしていて光沢もありません。
屋外で使用する構造物にはさほどこの見た目は影響しないかもしれませんが、溶融亜鉛メッキは屋内などで使用するものには少し意匠性が劣ります。なおかつ、電気亜鉛メッキのものはクロメート処理などによって色を付けることも可能ですので、組み立て時のヒューマンエラーを回避する目的で右ネジを黄色、左ネジを黒などと変えてご使用される場合もございます。
メッキの膜厚については、電気亜鉛メッキのほうがコントロールしやすくなり、精密部品などには適しています。薄板などのメッキに際しては、溶融亜鉛メッキはプロセスに熱を用いるため、変形することも考慮する必要があります。
5.おすすめの用途
5.1. 電気亜鉛メッキで効果が高い用途

ここまでご説明してきた性質の違いなどから、電気亜鉛メッキと溶融亜鉛メッキにはそれぞれに得意分野があることになります。
電気亜鉛メッキの場合、屋外の大型の部材のメッキには、耐用年数も少なく、適していません。その代わり、屋内で使用するような小型部品や精密部品については、膜厚もコントロールしやすく、適しています。
緻密で光沢のある見た目も、その傾向を手伝います。
クロメート処理などの後処理を活用すれば、そこから耐食性を上げるだけでなく、見た目の向上にもなります。
また、薄板のメッキであっても、熱による変形は起きません。
5.2. 溶融亜鉛メッキで効果が高い用途

溶融亜鉛メッキの場合、何と言っても特徴は厚い膜厚が可能なところです。
このことにより、屋外での耐用年数も期待できます。
屋外の構造物や建物のような大きな部品や製品へのメッキは、溶融亜鉛メッキのほうがはるかに適しています。なお、屋外で使用する構造物の中にネジや薄板のフランジなど溶融亜鉛メッキの苦手なものが含まれている場合、その部材に関しては電気亜鉛メッキのクロメート処理を行うことをお勧めします。
6. まとめ

電気亜鉛メッキと溶融亜鉛メッキの違いについて解説してまいりました。
以下はそのまとめです。
鉄素材などの耐食性を上げる方法として亜鉛メッキがあるが、亜鉛メッキには電気亜鉛メッキと溶融亜鉛メッキの2種類がある。
亜鉛メッキの防食の方式は犠牲防食である。
電気亜鉛メッキは電気を用いて亜鉛皮膜を付着させるメッキ方法で、あまり厚い膜厚を生成させることはできない。
亜鉛メッキの見た目や耐食性の向上のため、クロメート処理などの後処理を行うこともできる。
溶融亜鉛メッキは溶けた亜鉛が入った槽に素材を漬け込んで亜鉛皮膜を付ける方法で、厚い膜厚を生成させることができる。
犠牲防食のメッキの耐用年数はメッキの付着量に関係するため、膜厚の厚い溶融亜鉛メッキのほうが耐用年数が長い。
耐用年数の長い溶融亜鉛メッキは屋外の構造物向きで、電気亜鉛メッキは屋内の小型部品や精密部品に適している。
メッキ加工のプロフェッショナルに、まずはご相談を!
「この加工、どうしても上手くいかない…」「他社で断られてしまった…」「納期が迫っているけど間に合うか不安…」そんなお悩み、ぜひ株式会社コネクションにご相談ください!
私たちコネクションは、メッキ加工や表面処理加工のスペシャリスト集団です。他社では対応が難しいとされる案件も、多くの実績と専門知識を活かして対応してきました。
他社で断られた案件こそ、私たちにお任せください!
高度な技術力: 無電解ニッケルメッキをはじめ、アルマイト処理、特注ジグを使用した加工など、様々な技術で対応します。
迅速な対応: ご依頼いただいた内容について、1営業日以内に回答いたします。急ぎの案件も、最適な解決策をご提案します。
広範なネットワーク: 100社以上の協力メーカーとの連携により、自社で難しい場合も最適な方法を見つけます。
安心のサポート体制: 実績25年以上の電気メッキ技能士が直接対応。
「自分たちの案件は無理かも」と諦める前に、ぜひ一度お問い合わせください。コネクションのスタッフが、あなたの課題に真剣に向き合い、解決に向けた最善の方法をお届けします。
お問い合わせは簡単・スピーディー!
お電話やメールフォームから、どなたでも簡単にお問い合わせいただけます。案件の概要やお悩みをお伝えいただくだけで、当社の専門スタッフが迅速に対応します。
株式会社コネクションは、「どんなメッキの悩みもまず相談してみたい!」と思われる信頼のパートナーを目指しています。ぜひお気軽にご連絡ください!
めっきに関するお問合せやご質問はメールもしくはお電話にてお気軽にご連絡下さい。
お急ぎの方はこちら 直通電話 090−6819−5609
【著者のプロフィール】
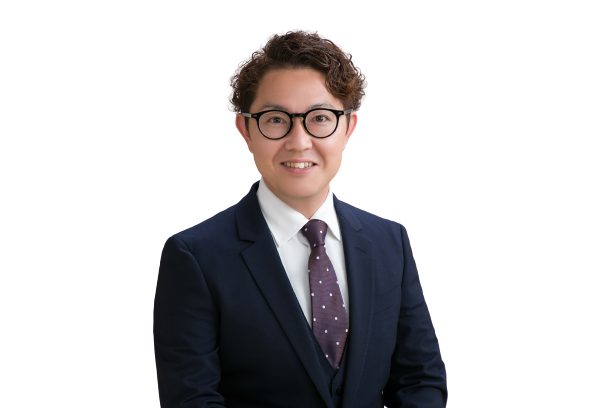
1996年、福井工業大学附属福井高等学校を卒業後、地元のメッキ専門業者に入社、製造部門を4年経験後に技術部門へ異動になり、携帯電話の部品へのメッキ処理の試作から量産立ち上げに携わる。
30歳を目前に転職し別のメッキ専門業者に首席研究員して入社。メッキ処理の新規開発や量産化、生産ラインの管理、ISO9001管理責任者などを担当。
コメント