【メッキのプロ直伝】無電解ニッケルメッキは高い皮膜硬度、均一性に優れたメッキですが、膜厚の管理はこのように行います。
- connectionfukui
- 2021年6月28日
- 読了時間: 9分
更新日:2023年10月15日
メッキは膜厚が重要です。メッキの性質は膜厚によっても変わることがあります。
例えば耐食性は膜厚が大きいほど上がる傾向にあります。ただし、製品自体の厚さもありますし、コスト面を考慮しても厚ければ厚いほどよいというものでもありません。製品に必要な耐久性を検討し、適切な膜厚を設定することも設計上重要となることがあるのです。無電解ニッケルメッキにおいても膜厚管理は重要です。
本記事では、無電解ニッケルメッキの実際の膜厚の管理方法をご紹介します。
また、図面などに記載されるJIS記号について、膜厚の表記には重要な注意点がありますので、合わせてご紹介します。
■INDEX■
・無電解ニッケルメッキとは
・皮膜の均一性
・膜厚について
・膜厚とメッキ時間
・膜厚の調整方法
① ダミーからメッキ時間を算出する方法
② ダミーと一緒にメッキを行う方法
・蛍光X線検査
・デジタルマイクロメータによる実寸の測定
・質量計測による方法
・断面観察
・図面におけるメッキのJIS記号
・膜厚の表記についての注意点
1.無電解ニッケルメッキの特徴
1.1.無電解ニッケルメッキとは

無電解ニッケルメッキとは、電解メッキと違い電極を使用せずに製品表面の化学反応のみを利用したメッキ方法です。メッキ液中の還元剤を利用し、金属を還元して皮膜を生成します。
生成された皮膜にはリンが含有され、その影響で耐食性が向上します。また、硬度も向上し、そのため耐摩耗性の向上も見込むことができます。
耐食性や耐摩耗性に利点があることから、無電解ニッケルメッキは例えば自動車部品等の分野で活躍しています。
1.2.皮膜の均一性
製品が複雑な形状をしていても、メッキ液中での反応にその差がでるわけではありませんので、製品のどの表面を見ても均一に皮膜が生成されることになります。
無電解ニッケルメッキは皮膜の均一性が極めて高く、そのことと耐食性や硬度でのメリットが合わさって、精密部品や電子部品等に使用されることも多いです。
1.3.膜厚について
例えば、無電解ニッケルメッキの耐食性は、皮膜のリンの含有率にも左右されるものですが、膜厚の厚さによっても異なります。膜厚が厚いほど製品の耐久性も増しますし、ピンホールなどの影響で錆が発生するリスクも減少します。
一方で、寸法的な問題や経済性から、膜厚を大きく取れば取るほどよいわけでもなく、設計者は使用する環境に応じて適切な膜厚を設定することが重要です。
2.無電解ニッケルメッキの膜厚の調整方法
2.1.膜厚とメッキ時間

メッキの中で極めて重要なファクターである膜厚ですが、無電解ニッケルメッキの膜厚はどのように設定するのでしょうか?ここではその調整方法について解説します。
無電解ニッケルメッキの場合、還元剤から析出される物質の量は化学反応に要する時間に比例します。この化学反応の速度は析出速度と言いますが、メッキ液のpHや温度によって変わります。つまり、無電解ニッケルメッキの膜厚は、同じメッキ液でメッキをすれば、メッキ浴で反応させているいわゆる浸漬時間に比例します。したがって、膜厚は時間を計測することで管理することができます。
なお、無電解ニッケルメッキは電解メッキと比べて析出速度が遅く、その分、均一にメッキできる一方でメッキに要する時間は長くかかってしまいます。
2.2.膜厚の調整方法
① ダミーからメッキ時間を算出する方法
2つの方法はいずれも製品とは別にダミーの試験片を使用します。
1つ目の方法は、製品のメッキ前にダミーで試験メッキを行います。ダミーを規定時間メッキしたら、その膜厚を計測し、実際の製品の膜厚に要する時間を算出します。この得られたメッキ時間でメッキを行うことで、ほとんど誤差もなく所定の膜厚に仕上げることが可能です。
② ダミーと一緒にメッキを行う方法
もう1つの方法では、ダミーと製品を一緒にメッキします。
ダミーの膜厚を適宜計測し、指定の膜厚になって時点でメッキを終了させます。無電解メッキはダミーと製品が同じように皮膜を析出するため、この方法でも、製品はほぼ誤差なく指定の膜厚に仕上がります。
これらのダミーを用いた方法は、メッキ時に均一さが保証されない電解メッキでは不可能な方法で、無電解メッキならではの管理方法です。
3.無電解ニッケルメッキの膜厚の確認
では実際の製品の膜厚を確認するにはどうすればよいのでしょうか? ここではいくつかメッキ膜厚の確認方法をご紹介します。
3.1.蛍光X線検査
放射されるX線のエネルギーは物質によって異なるので、それによってどの物質が含有されているかを調べることができます。また、各X線のエネルギーにおけるX線強度はその物質の含有量が大きければ強くなります。
メッキの膜厚を調べる場合、膜厚が厚ければ皮膜の物質に相当するX線の線量が大きく計測され、素材の物質に相当するX線の線量は小さくなります。この線量を計測して膜厚を計測する方法が蛍光X線検査です。
多層膜であっても、個別にX線エネルギーが検出されるため、同時に測定することができます。また、無電解ニッケルメッキは均一性が高いものの、複数点を計測することでメッキのムラを検査することも可能です。
測定するためには専用の装置が必要で、定置型のものやハンド型のものなどさまざまありますが、いずれも他の方法に比べると装置が少し高額になります。
3.2.デジタルマイクロメータによる実寸の測定
従来は回転方向に目盛りを表示してそれを読み取っていましたが、最近のものはデジタルで測定できるデジタルマイクロメータが広く導入されています。
無電解ニッケルメッキの膜厚を測定する場合、あらかじめ素材の厚さを計測しておき、メッキ後に同じ箇所の厚さを測定することで、その差を膜厚として得ることができます。
無電解ニッケルメッキは皮膜の均一性が高いため、(メッキ後の測定結果-メッキ前の測定結果)/2でほぼ正確な膜厚が算定されます。この方法は、精密な単位まで計測できるマイクロメータならではの方法です。
蛍光X線検査同様、非破壊で測定することができる上に、比較的簡易的な測定で膜厚がわかります。
ただし、蛍光X線検査のような成分の分析や多層膜への対応は難しいです。
とはいえ、膜厚を調べるだけならこの方法が最もシンプルで、広く使用される方法です。
3.3.質量計測による方法
質量はメッキ前後で、メッキの膜厚の分だけ重くなります。つまり、質量の差が付着した皮膜の合計の質量ということになります。
メッキの表面積が算定しやすいものであれば、この質量の差を表面積で割り、さらにメッキ成分の密度で割ってやれば、膜厚の値を得ることができます。
厳密に言えばここで得られる厚さは平均値ですが、無電解ニッケルメッキは均一性が高いため、ほぼ正確な膜厚として捉えることができます。ただし、複雑な形状で表面積が算出しにくい製品には不向きな方法になります。
3.4.断面観察
ここで紹介している方法の中では唯一の破壊検査で、そのため切断した製品は測定用としてしか活用できません。つまり、ダミーや予備個数がある場合しか採用できない方法です。
どちらかと言えば、膜厚の測定にとどまらず、断面の状態などを詳しく分析したいときに用いる方法で、また、当然切断した面の膜厚のみしか得ることはできません。
4.図面内のJIS記号での膜厚について
無電解ニッケルメッキにおいては、所定の膜厚を精度高く、均一に実現できることがおわかりいただけたと思います。設計者はこのことを踏まえ、用途や機能に合わせてメッキの膜厚を検討し、それを製品に反映させる必要があります。
JISでは図面内等に表記するメッキ記号があり、膜厚の表記方法もありますので、ここでご紹介します。
4.1.図面におけるメッキのJIS記号
メッキのJIS記号による表記は例えば、製品の図面に「ELP-Fe/Ni(90)-P5」といった形で記載されています。この例ですと、「鉄素材の無電解ニッケル(90%)-リンメッキで膜厚5μm以上」という意味となります。
ひとつずつを紐解くと、「ELP」は無電解メッキの意味、「Fe」は鉄素材という意味、「Ni(90)-P」はニッケル(90%)とリンの合金メッキという意味、最後の「5」がメッキの膜厚5μm以上を意味します。これらは全てJISで規定された記号の定義ですが、図面の中ではしばしば、このようなメッキの表記(記号)を記載します。
設計者はこのJIS記号でメッキ業者にその方法などを図示して指定し、メッキ業者はそのとおりにメッキを行います。つまりこの表記は重要な情報共有となるのです。
ただしこの中で、設計者とメッキ業者双方でよく誤解が起こる箇所があります。
4.2.膜厚の表記についての注意点
誤解の多いメッキのJIS記号、それは最後のメッキ膜厚の記号部分です。まさに本記事で解説してきた内容の部分で、記事内でも何度も述べたとおり、本来は膜厚はとても重要なパラメータです。
誤解が多いのは、例えば先の例で言うと「5μm以上」の「以上」の部分です。
JISで規定されているのは、膜厚を最後に記載される数値以上で行うという意味で記号を設定しています。ところが、これをピンポイントの5μmちょうどと誤解したり、5μmがプラスマイナスの公差の中央値と勘違いしている人が意外に多いようです。
仮に設計者が誤解してしまっていれば、本来5μmちょうどでメッキされていないと寸法上整合しないものが7μm程度で仕上がってしまうといったトラブルが起きてしまいます。
メッキ業者が誤解してしまう場合、設計者がせっかく少なくとも5μmないと耐食性が足りないと考えてそのような記号を記したのに、4.5μmで仕上がってしまい、耐食性が足りなくなってしまうというトラブルも起きてしまいます。
概ね、正しい理解のもとでは、このような記号で指定されている場合は6~8μmの膜厚で仕上げられることが多いです。
正確な情報共有を行い、トラブルを防ぐためにも、このメッキのJIS記号、特に「以上」という表現は誤解しないようにしていただきたいところです。
5.まとめ
今回は無電解ニッケルメッキの膜厚について、メッキ時の管理方法や測定方法、図面に表記する際の注意点などをご紹介しました。以下まとめです。
無電解ニッケルメッキでは電極の影響を受けないため、複雑な形状でも皮膜は均一に付着する。
皮膜の均一性を利用し、無電解ニッケルメッキでは、ダミーを利用して時間を計測して膜厚を設定する方法やダミーと一緒にメッキを行う方法で正確な膜厚管理を行うことができる。
膜厚を確認するための測定方法としては、蛍光X線検査、デジタルマイクロメータによる測定、質量計測による方法、断面観察などがあるが、デジタルマイクロメータによって実寸を測定する方法が最もポピュラーである。
メッキの膜厚をJIS記号により図示することは設計者にとってもメッキ業者にとっても重要な情報共有だが、この膜厚表記は数値以上という意味であることを理解することが重要である。
お急ぎの方はこちら 直通電話 090−6819−5609
【著者のプロフィール】
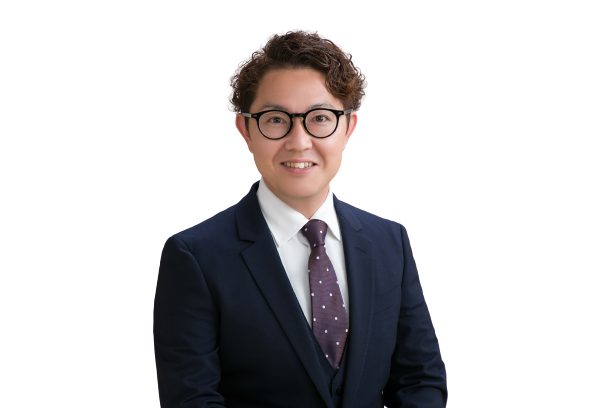
1996年、福井工業大学附属福井高等学校を卒業後、地元のメッキ専門業者に入社、 製造部門を4年経験後に技術部門へ異動になり、携帯電話の部品へのメッキ処理の試作から量産立ち上げに携わる。
30歳を目前に転職し別のメッキ専門業者に首席研究員して入社。 メッキ処理の新規開発や量産化、生産ラインの管理、ISO9001管理責任者などを担当。
コメント